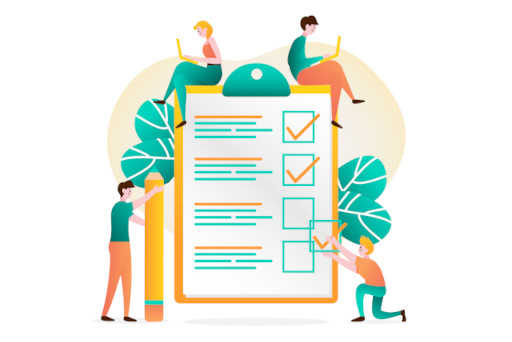
In the realm of quality management, Corrective and Preventive Actions (CAPA) form a cornerstone of ISO 9001 compliance. These measures are essential for maintaining the integrity of an organization’s processes and ensuring continuous improvement. In this blog, we’ll explore CAPA’s role in ISO 9001, its requirements, and how businesses can achieve compliance effectively.
What is CAPA in ISO 9001?
CAPA stands for Corrective and Preventive Actions, two distinct but interconnected processes aimed at identifying and addressing issues in a way that improves quality management systems (QMS).
- Corrective Action: This involves identifying and eliminating the root cause of an existing issue to prevent its recurrence.
- Preventive Action: This focuses on proactively identifying potential issues and implementing measures to prevent their occurrence.
ISO 9001:2015 emphasizes the importance of risk-based thinking and continual improvement, making CAPA a critical tool for achieving and maintaining these goals.
CAPA Requirements in ISO 9001
ISO 9001 does not explicitly use the term CAPA in the 2015 revision. However, its principles are embedded in various clauses that highlight corrective and risk-based actions. Here are the key sections related to CAPA:
- Clause 10.2: Nonconformity and Corrective Action
- Organizations are required to identify nonconformities, take corrective actions to address them, and prevent recurrence.
- The process includes:
- Reacting to nonconformities and mitigating their impacts.
- Determining the root cause.
- Implementing and reviewing corrective actions.
- Clause 6.1: Actions to Address Risks and Opportunities
- While this clause focuses on preventive thinking, it aligns with the concept of proactive measures to address potential risks before they materialize.
- Clause 9.1: Monitoring, Measurement, Analysis, and Evaluation
- Organizations must monitor and measure QMS performance to identify areas for improvement, triggering CAPA processes when necessary.
- Clause 10.3: Continual Improvement
- CAPA plays a vital role in driving continual improvement by addressing issues and refining processes.
Steps to Implement CAPA for ISO 9001 Compliance
A well-structured CAPA process ensures ISO 9001 compliance while fostering a culture of improvement. Here’s a step-by-step approach:
- Identify and Document Nonconformities
Capture all instances of nonconformity systematically. Documentation should include details about the issue, its impact, and how it was identified
- Perform Root Cause Analysis
Use proven techniques such as the 5 Whys, Fishbone Diagram, or Failure Mode and Effects Analysis (FMEA) to determine the root cause of the issue. This ensures actions target the underlying problem, not just the symptoms.
- Plan Corrective or Preventive Actions
Develop a detailed action plan that:- Addresses the root cause.
- Assigns responsibilities for implementation.
- Includes timelines for completion.
- Implement Actions
Execute the planned corrective or preventive measures. Ensure all relevant stakeholders are informed and involved.
- Verify Effectiveness
Monitor and measure the outcomes of implemented actions to confirm their effectiveness. If issues persist, revisit the root cause analysis.
- Update Documentation
Record all findings, actions taken, and verification results. This documentation is crucial for audits and internal reviews.
Common Challenges in CAPA Implementation
While CAPA is integral to ISO 9001 compliance, organizations often face challenges, such as:
- Inadequate Root Cause Analysis: Failing to identify the true root cause can lead to ineffective actions.
- Poor Documentation: Incomplete records can hinder audits and compliance efforts.
- Lack of Follow-Up: Without verifying effectiveness, CAPA efforts may fail to achieve desired outcomes.
- Overlooking Preventive Actions: Many organizations focus heavily on corrective actions and neglect the proactive aspect of CAPA.
Best Practices for CAPA in ISO 9001
To overcome these challenges and maximize the impact of CAPA, consider the following best practices:
- Invest in Training: Equip your team with the skills and tools needed for effective root cause analysis and CAPA implementation.
- Leverage Technology: Use QMS software to streamline CAPA tracking, documentation, and reporting.
- Foster a Quality Culture: Encourage employees to report nonconformities and participate in continuous improvement efforts.
- Integrate CAPA into Risk Management: Align CAPA efforts with the organization’s risk management processes for a proactive approach.
Conclusion
Corrective and Preventive Actions (CAPA) are essential for compliance with ISO 9001, helping organizations address non-conformities and drive continuous improvement. By integrating CAPA into the Quality Management System, organizations can ensure compliance, achieve sustainable improvements, and maintain high-quality standards.
Developing a strong approach to CAPA management is a crucial step in enhancing the effectiveness of the QMS and supporting continuous improvement goals, contributing to greater efficiency and long-term sustainability.